Maintenance at a pharmaceutical plant
The challenge: increasing collaboration and reducing paperwork.
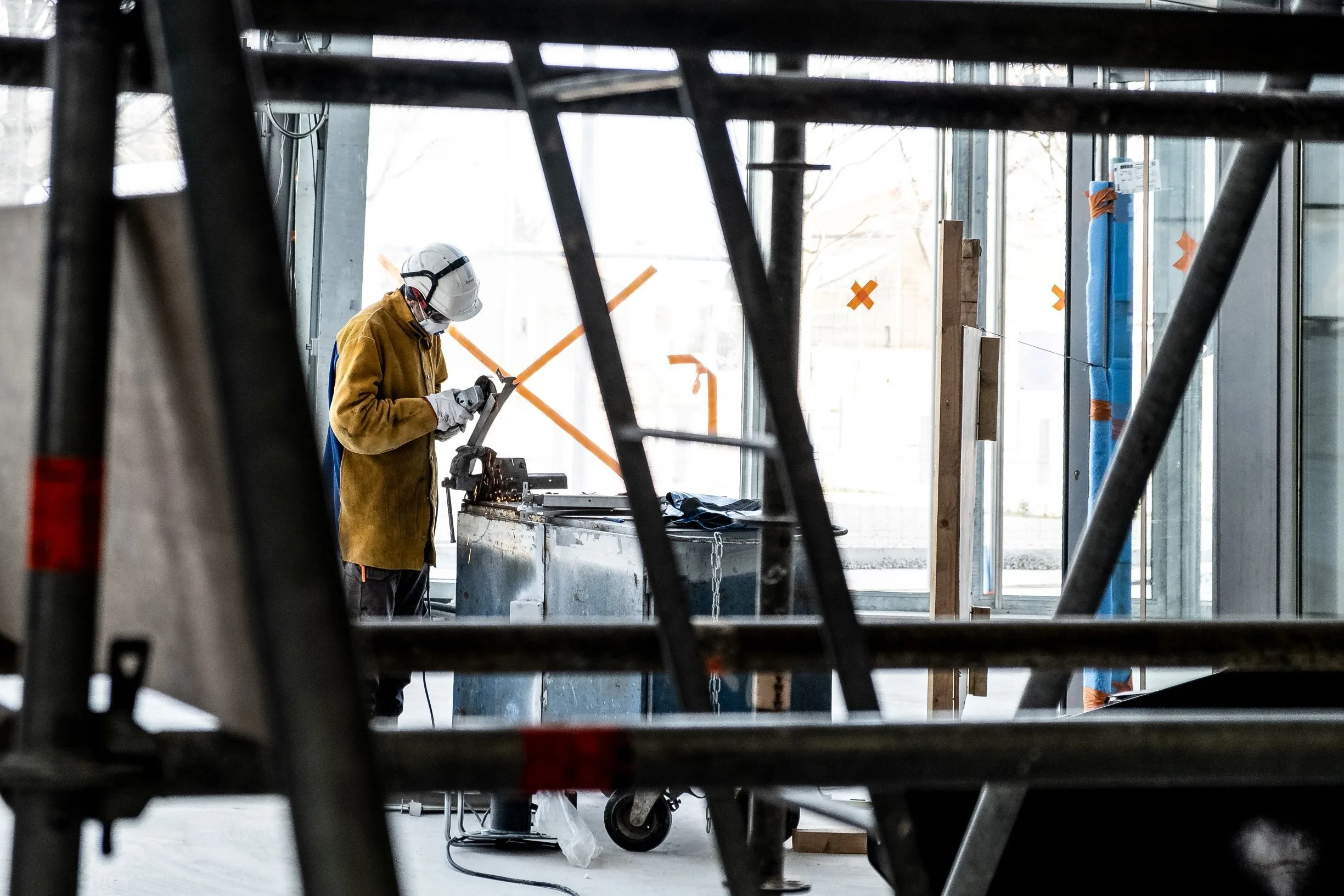
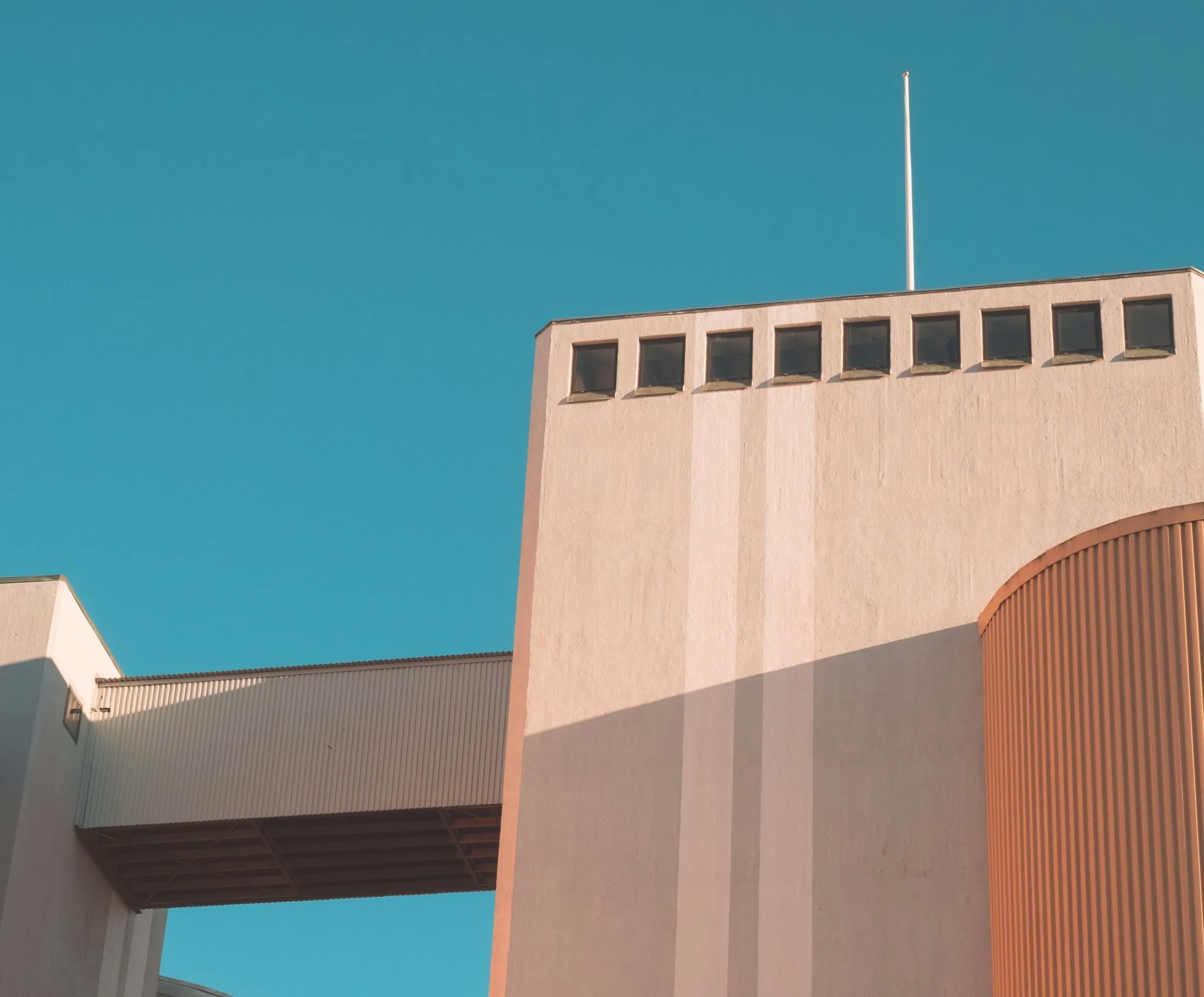
01
Problem and Approach
‘’The plant personnel uses SAP to manage maintenance activities. Multiple tools were used in parallel: paper, e-mail, WhatsApp, MS Office; but real-time tracking and knowledge management remained a big challenge.’’
A step forward
Coordinating field maintenance using Mela, a chat that organizes information as an enterprise asset management system.
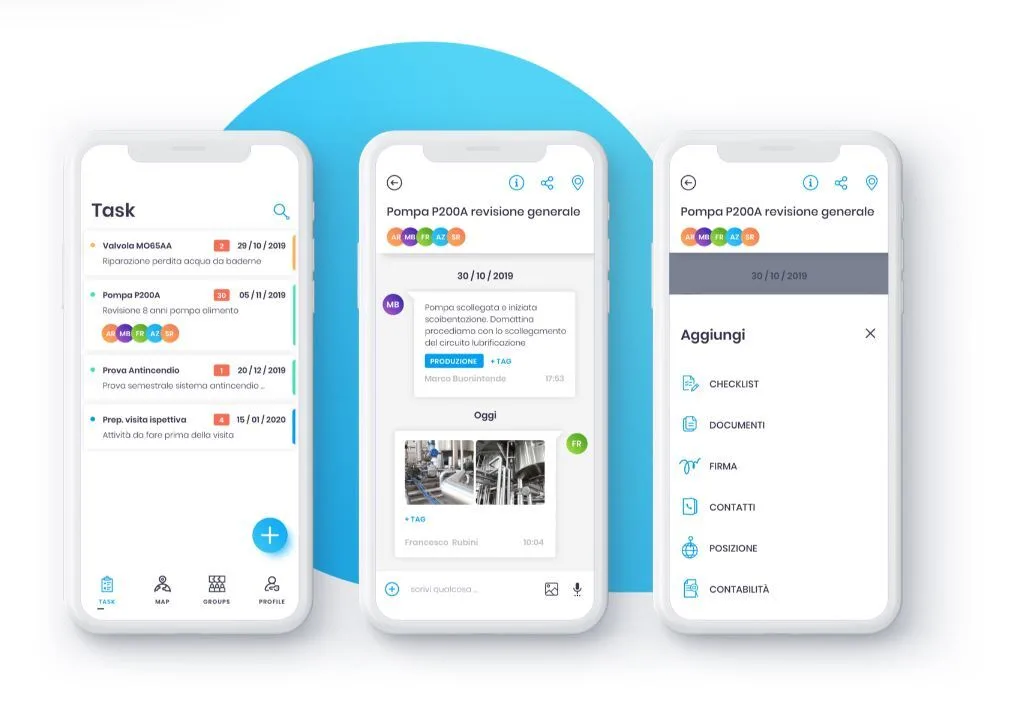
Benefits
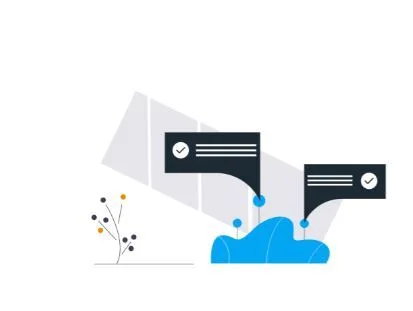
Information
o All the stakeholders (Operations, Maintenance, Safety, etc.) easily collaborate using a chat interface.

Cross-company sharing
o Mela becomes the operational bridge between maintenance contractors and plant management, ensuring continuous tracking and enabling real-time reporting.
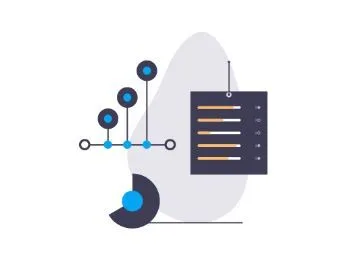
Knowledge
o Manage the impact of personnel attrition and generational change: knowledge stays in the company through the Mela database generated from the field.
02
Case Study
What has been done?
Production Facility
Pharmaceutical plant in Northern Italy
1 production facility
67,000 m2
200+ people
02
Case Study
What has been done?
-
January 2019
Mela launch for the utilities maintenance team
-
June 2019
Mela is implemented to follow the construction and commissioning of a new production line
-
September 2019
Mela is extended to the maintenance contractors
Mela Usage
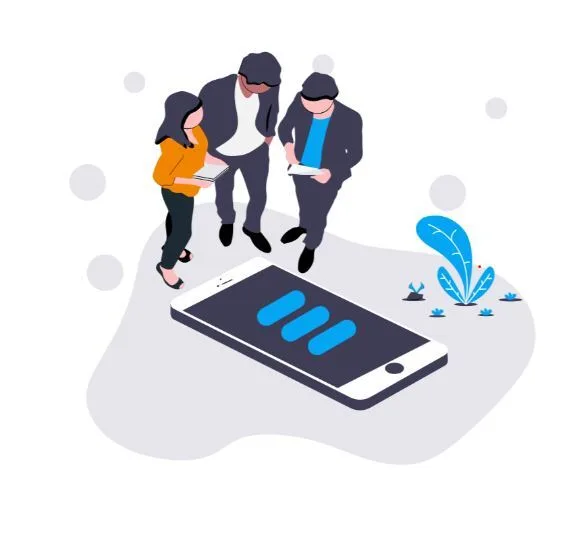
- Maintenance work coordination
- Field procedures
- Inspections and walkarounds
- Contractor logbooks
- Manintenance reports
- Automated contract progress reports
Instant messaging for the industrial sector
- Specific features like checklists, people and materials accounting, were developed to follow existing processes.
- All functionalities are perfectly integrated into the chat interface, maintaining a familiar user interface, and making training quick and easy.
- Data can be accessed from the office through the web portal. A powerful search makes it easy to retrieve old data, and reporting is done with one click.
03
Implementation
What really changes?
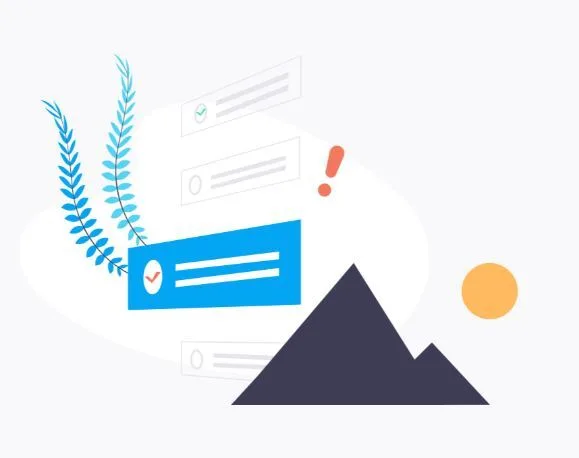
A bridge across departments and companies
Mela goes beyond the common maintenance software, putting a chat at the center of all the activities: it’s like using a WhatsApp group for each work task. All the stakeholders are involved, creating a touchpoint between your team, contractors, and other relevant departments.
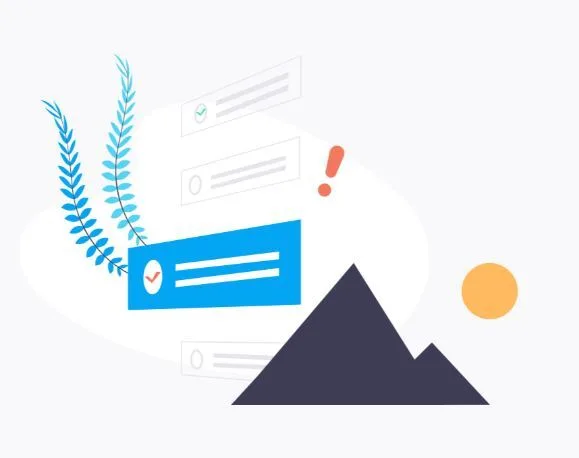
A chat on steroids!
“We were using WhatsApp to collaborate and solve problems, but then we had to fill a bunch of forms to comply with company processes.”
The Mela chat contains all checklists, signatures, accounting items, tags, photos, videos, and documents.
Both structured data (measurements, procedures, checks) and unstructured information (communication between people around issues) is therefore managed through a single platform.
This simplifies work and brings it closer to the day-to-day reality in the field.

"Writing reports? A thing of the past."
“After a job is done, we must prepare a work report, but there is never enough time. As our most experienced colleagues will soon retire, it’s important to transfer their knowledge to the next generation. We tried archiving MS Word reports in a shared drive, but it was time consuming and when you search for something it’s very difficult to find what you are looking for.”
The Mela chat becomes a company archive: organized, secure, forever available.
Information is collected in the field with the speed and flexibility provided by the transcribed voice messages, pictures, and videos.
The inserted data can be edited, approved, or frozen adapting to process requirements.
Work, quality and progress reports are generated with one click.
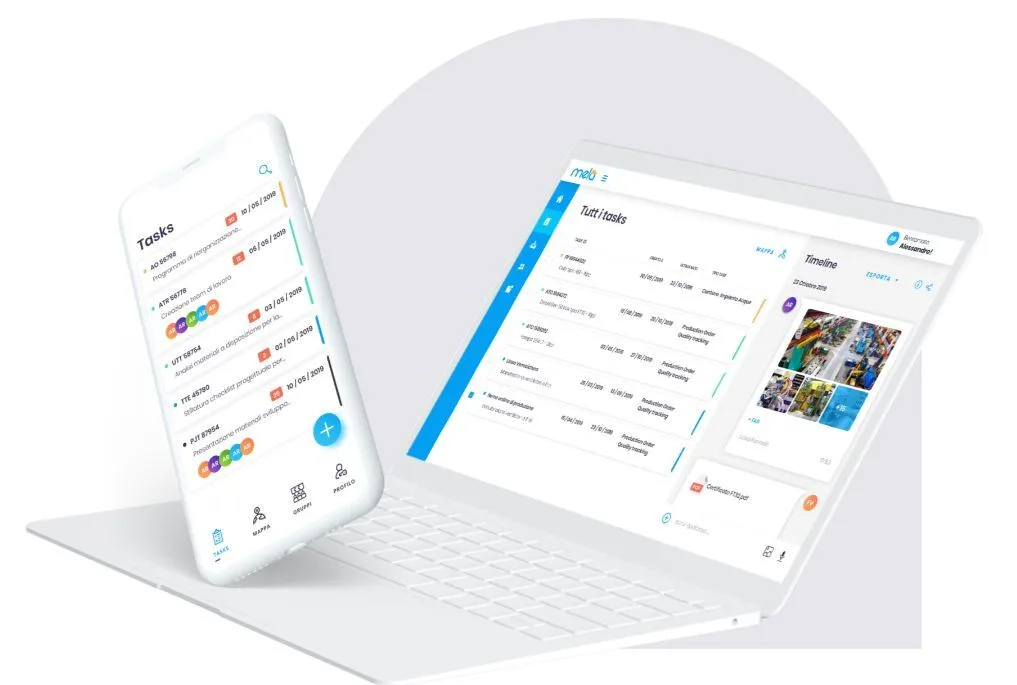
Go-live in 48h
50%
time saved organizing work and generating reports
30%
errors and rework reduction
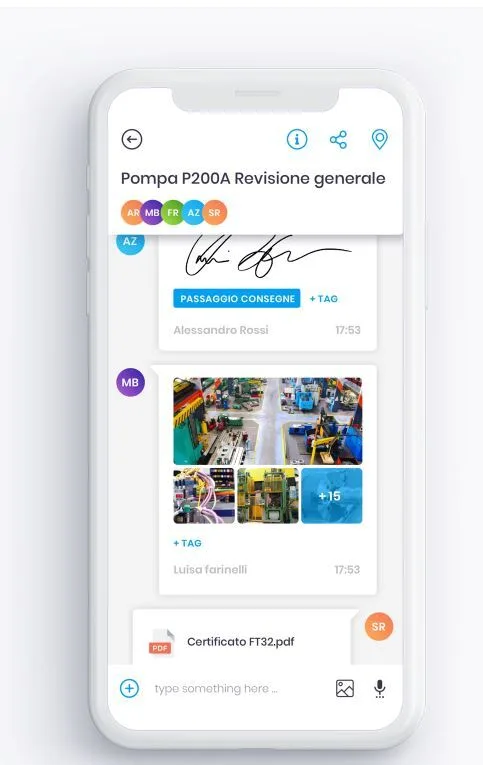
04
The Numbers
From theory to practice
Smooth, effective work management
One of the biggest changes has been the increased time spent on the work site by managers and supervisors. Their added value increases when they can be in the field instead of generating paperwork. That has made processes leaner, increasing wrench time and decreasing the time spent in meetings.
Leveraging contractors
Mela improves contractor management: the work can be assigned, tracked, and approved using the same tool. Information between parties become precise and consistent, and when it comes to paying contractors at the end of the month, all the needed information can be gathered in a few minutes.
Contractors particularly appreciated this new approach, because it reduced the time needed to generate reports and it facilitates payments. Some of them even started using Mela to manage their work with other clients.
From maintenance to construction and commissioning
“Why stop with existing plants? We were about to begin the construction of a new production line, and we needed to track the building and commissioning of the new assets in order to capture and preserve valuable knowledge for the asset life cycle.”
Mela was used to keep track of the construction activities, and it allowed us to significantly reduce the time needed to make the new line fully operational.
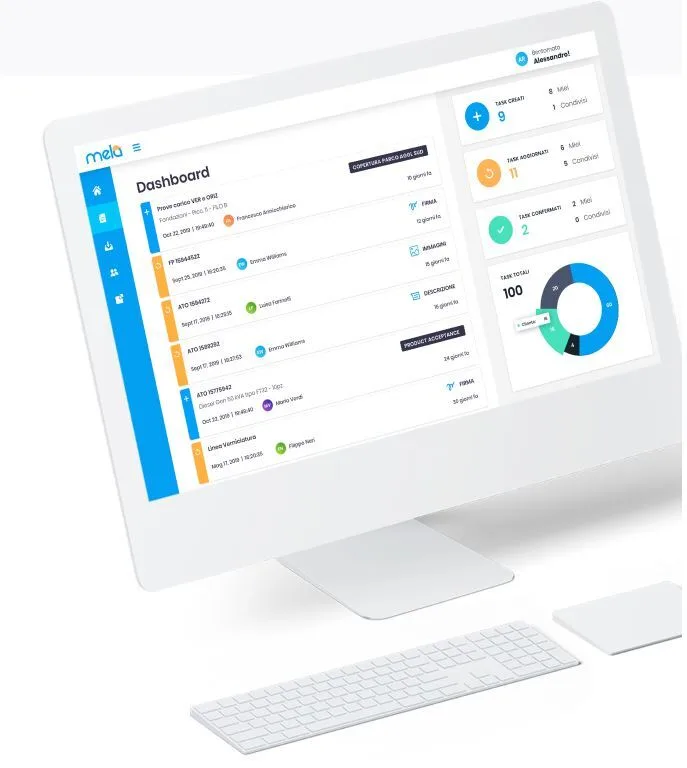